


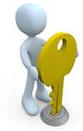 |
PTC耐冲击性能的研究
1 概述
近年来,陶瓷PTC热敏电阻器作为一种重要的自愈限流元件,越来越受到重视与发展, 因此而导致的BaTiO3陶瓷PTC热敏电阻器限流元件的研究亦就日益深入。目前,应用最广泛的陶瓷PTC热敏电阻器,是在BaTiO3为主晶相的钙钛型ABO3结构中,通过添加居里点移动剂、施主元素、受主元素、玻璃相以及改性添加剂制备而成;其中尤以改性添加剂的作用成为陶瓷PTC热敏电阻器研究的重要课题。
谈到改性添加剂,也就不能不说说作为提高PTC耐电压性能添加剂的CaCO3, 以证明改性添加剂的“双刃剑”效应:1986年,原715厂陈龙虎高级工程师通过研究与实验,在PTC消磁热敏电阻器的批量生产中添加适量的CaCO3从而大幅度提高了产品的耐电压能力, 为后来715厂从日本TDK公司技术引进PTC消磁热敏电阻器生产线奠定了前期的技术基础;可以这么说——那是715厂BaTiO3陶瓷PTC消磁热敏电阻在量产过程中提高产品耐电压性能的一个里程碑! 时值今日,CaCO3仍作为提高PTC耐电压性能的添加剂而被广泛应用。然而,即便是生产了近20年的PTC消磁热敏电阻器,随着品种与质量要求的进化,其
-20°C断续寿命试验时出现分层失效的技术问题依然困惑着大多数生产厂家!同时,随着通讯保安单元中起二级保护作用的PTC热敏电阻器限流元件(以下简称:PTC)市场需求的上升,国内众多PTC生产厂家因不能有效解决其失效模式(650VAC,起始电流1.1A,通电1分钟,断电10分钟,重复10次,阻值变化率小于20%)检验时出现的机械分层现象,被挡在了市场之外。通过实验, 认为这与片面大量添加CaCO3有关(在PTC结构设计合理的前提下),这正是下面本文所探讨的问题之一: 大量添加CaCO3所带来的负面效应——电压效应增强、抗功率冲击能力下降。
本文所言的“功率冲击”是:PTC热敏电阻器在通电后,由初期的I。下降到平衡电流时,所承受的电功率变化以及由之所导致的热功率变化的总和。鉴于PTC所具有的时间—电流特性,“功率冲击”在这里特指:PTC热敏电阻器从通电起始至达到热平衡前的功率骤变总和。
2 实验证明
2.1原材料、配方与工艺
实验所使用的主要原材料见表1。
表1
材料名称 |
纯度(%) |
BaCO3 |
99.75 |
SrCO3 |
99.5 |
CaCO3 |
99.35 |
TiO2 |
99.5 |
Y2O3 |
99.99 |
SiO2 |
99.99 |
Mn(NO3)2 |
50 |
欧姆铝浆 |
中温 |
表层银浆 |
中温 |
实验初期所采用的配方为:
(Ba76-xmol%Sr6mol%Ca18mol%Yxmol%)Ti100+Amol%O3++SiO2Bwt%+Mn(NO3)2 Cwt%。
式中:
X=0.3~0.6,A=0.5~2.5,B=0.3~1.0,C=0.015~0.03,B&C按氧化物总重计算。
工艺流程:
秤量→调和→脱水→合成→球磨→脱水→造粒→干燥→成型→烧结→电极→焊接→包封→→测量
工艺说明如下:
“调和”——湿式球磨。将表1中固体材料按配方要求的质量一次性全部投入球磨罐中,加入材料总重1.5倍的纯水,再按配方要求加入制好的Mn(NO3)2溶液并进行球磨混料。
“合成”——1150°C保温3小时。
“造料”——粘合剂浓度:15%,添加比例---材料:PVA=100g:15ml。
“成型”——Φ9.35×t2.35mm×0.532g/片。
“烧结”——升温速率:300°C /hr,烧结温度:1330°C,保温时间:1小时,降温到800°C的速率:100~200°C/hr。
“电极”——先印刷并在650°C烧渗欧姆铝电极,再在铝电极上印刷烧渗(550°C)表层银电极。
“焊接”——手工焊接Φ0.5CP导线,焊接液相点:294°C。
“包封”——浸涂并聚合改性有机硅包封料。
2.2 实验产品的相关指标
瓷体尺寸:
Φ8.0×t2.0mm,电阻值:R25=55±20%Ω,居里温度:90~95°C,温度系数:20~30°C/%(由居里温度+15°C和居里温度+25°C所对应的电阻值所求得),伏安特性:Vb=900VAC
Imin=2.8mA VImin=650VAC。
2.3 PTC失效时的表象
PTC在承受650VAC、1.1A功率冲击(通电1分钟,断电10分钟,重复10次)时, 其基体边缘的中部在初期通电过程中就会出现电孤,并伴有微弱的声音会出现,有的产品甚至在两次冲击后就产生明显机械分层的现象, 也有部分产品在冲击循环完成后,稍微承受微弱的外力即沿电孤部位分成两片,且分层的断面较为平整、均匀。
3 分析
3.1从伏-安特性来分析
为什么PTC在伏-安特性测试时的耐电压能力达到900Vac、 但产品却在650VAC、1.1A的冲击中就出现失效?为此,笔者设计了一个理想状态下的伏-安曲线与阻-温曲线对照的分析模式,基本思路是:按照欧姆定律,用伏-安特性中的电压V除以对应的电流I,得出的电阻值曲线与阻-温曲线(零功率状态下测得)比较, 结果非常明显:计算并绘出的阻-温曲线较阻-温特性测试出的电阻值曲线(零功率状态下测得)出现了较大的衰减,特别是Rmax。需要特别说明的是:计算出的Rmax’=(VImin/Imin),ΔR=Rmax-Rmax’。这证明了该PTC的电压效应非常明显。也就是说:产品实际承受电压的能力,并不是在步进加压条件(最大步幅为100Vac)下所测得的伏-安特性中的耐电压!
3.2从时间-电流特性来分析
笔者以250Vac、起始电流3A的条件测量了上述PTC的时间-电流特性, 发现产品而从起始状态I0到I0/2的过程不超过0.2秒,而从I0/2下降到I0/10所耗用的时间更是极短(不超过50毫秒);根据PTC在通电后发热致使其自身电阻值此跃升的原理,不难推断:施加在PTC上的电压从165VAC上升到241.5VAC的时间低于250毫秒
;.同理,PTC在650VAC、1、1A功率冲击时,由于PTC居里温区内的电阻值随温度变化呈指数级上升的特性,将导致PTC上876.94%的电压变化会在低于0.25秒的时间内完成,这对PTC瓷体来说,无疑是一种灾难,见表2。
由表2可以看出,从I0到I0/5的电压变化率较大,尤其是从I0到I0/2的电压变化率最大, 也就是说:PTC居里点拐点区是产品承受功率冲击最大的区间。
表2
V=250VAC,I0=3A |
数据 |
V=650VAC,I0=1.1A |
数据 |
起始I0时PTC上的电压(VAC) |
165.00 |
起始I0时PTC上的电压(VAC) |
60.50 |
I0/2时PTC上的电压(VAC) |
207.50 |
I0/2时PTC上的电压(VAC) |
355.25 |
I0/3时PTC上的电压(VAC) |
221.67 |
I0/3时PTC上的电压(VAC) |
453.50 |
I0/4时PTC上的电压(VAC) |
228.75 |
I0/4时PTC上的电压(VAC) |
502.63 |
I0/5时PTC上的电压(VAC) |
233.00 |
I0/5时PTC上的电压(VAC) |
532.10 |
I0/6时PTC上的电压(VAC) |
235.83 |
I0/6时PTC上的电压(VAC) |
551.75 |
I0/7时PTC上的电压(VAC) |
237.86 |
I0/7时PTC上的电压(VAC) |
565.79 |
I0/8时PTC上的电压(VAC) |
239.38 |
I0/8时PTC上的电压(VAC) |
576.31 |
I0/9时PTC上的电压(VAC) |
240.56 |
I0/9时PTC上的电压(VAC) |
584.50 |
I0/10时PTC上的电压(VAC) |
241.50 |
I0/10时PTC上的电压(VAC) |
591.05 |
从I0到I0/2的电压变化率(%) |
25.76 |
从I0到I0/2的电压变化率(%) |
487.19 |
从I0到I0/3的电压变化率(%) |
34.34 |
从I0到I0/3的电压变化率(%) |
649.59 |
从I0到I0/4的电压变化率(%) |
38.64 |
从I0到I0/4的电压变化率(%) |
730.79 |
从I0到I0/5的电压变化率(%) |
41.21 |
从I0到I0/5的电压变化率(%) |
779.50 |
从I0到I0/6的电压变化率(%) |
42.93 |
从I0到I0/6的电压变化率(%) |
811.98 |
从I0到I0/7的电压变化率(%) |
44.16 |
从I0到I0/7的电压变化率(%) |
835.18 |
从I0到I0/8的电压变化率(%) |
45.08 |
从I0到I0/8的电压变化率(%) |
852.58 |
从I0到I0/9的电压变化率(%) |
45.79 |
从I0到I0/9的电压变化率(%) |
866.12 |
从I0到I0/10的电压变化率(%) |
46.36 |
从I0到I0/10的电压变化率(%) |
876.94 |
3.3从阻-温特性来分析
按照3.1的分析方法,笔者发现:以前述配方和工艺制备的PTC,其电压效应与产品的温度系数存在很大的相关性——温度系数越大,ΔR越大,也就是说电压效应越明显。并且PTC居里点拐点区的过度越陡。
3.4从瓷体的热特性来分析
由3.2的分析可以看出:PTC上的电压骤升将导致PTC陶瓷基体承受骤然温升的热冲击。由于PTC的发热过程是源于平行其电极面的中心层面,通过热传递的方式使其整体达到热平衡的过程[2]。由此可以推断:PTC陶瓷基体的热特性是决定其在承受功率冲击时发生失效的关键因素之一,这主要反映在PTC陶瓷基体的热传导率、热膨胀率方面;同时,还必须从其抗热震性的观点出发,考虑陶瓷基体的物理结构[3];换句话说,如果PTC陶瓷基体的结构致密,具有热传导率低、热膨胀高的物理特性,势必导致其抗功率冲击能力下降的结果。
另外,PTC的直径厚度比与其抗功率冲击能力有着密切的关系,笔者发现:当直径厚度比大于5时,PTC的抗功率冲击能力可以得到提升,这应该还是与产品的热特性和热环境有关。
3.5从BaTiO3的固有特性来分析
首先,BaTiO3系PTC的PTC效应过程中存在四主晶相与立方晶相的(可逆)转变过程。同时,作为铁电相的BaTiO3陶瓷,还具有X和Y轴的电致伸缩现象[4], 这两种物理效应的综合结果就是:PTC在进行功率冲击时,受到了机械应力的作用;一旦机械应力主要产生于平行其电极面的中心层面并沿垂直于中心层面的方向传递,必将加速PTC在承受功率冲击时的失效。
综上所述,PTC在承受功率冲击时所出现的分层失效,其失效机理为:失效起源于PTC居里温区的初期,由于居里温区内PTC的电阻值随温度的变化呈指数级跃升,导致施加在PTC上的电压发生骤升,由此而引起的热突变、晶相转变以及电致伸缩所产生的热应力和机械应力的综合,是导致PTC出现分层失效的内在因素。
4 解决方案
4.1 降低电压效应
根据上述的分析结论,笔者重点从降低PTC的温度系数、保持耐电压能力的角度着手调整了配方体系:降低受主元素的添加量,增加施主元素并调整过量TiO2的添加量,但效果并不明显。
于是,笔者重新审视了CaCO3的添加量, 发现PTC在伏-安特性中的耐电压能力基本随CaCO3添加量的增加而提高,但其电压效应却同时呈现变强的趋势!这主要显示在伏-安特性中的VImin不变而Imin却上升,也就是说:由二者计算出的Rmax下降(当VImin为650V时,Imin由2.2mA上升到2.8mA就会导致Rmax’下降63.3KΩ)。对此,至少可以确定:在本配方体系中,CaCO3的添加量是影响PTC电压效应的重要因素之一。
为此,采用了Sr、Pb共加的配方体系,将CaCO3使用量降低到5mol%以下,结果是令人振奋的,详见表3。由实验数据分析可以明确两点:
1)Sr、Pb共加可以降低PTC的电压效应;
2)Sr、Pb共加同样可以获得高的PTC耐电压能力。
表3
项 目 |
原 配 方 |
Sr、Pb共加后,添加5mol%的CaCO3 |
尺寸(mm) |
Φ7.97хt1.98 |
Φ7.98хt1.97 |
R25(Ω) |
48~60 |
48~60 |
VB(VAC) |
900 |
950 |
VImin(VAC) |
600~650 |
650~800(持续) |
Rmax’(Ω) |
1.97E+05 |
3.54E+05 |
Imin(mA) |
2.8~3.3 |
2.2~2.4 |
Tc(℃) |
93 |
107 |
a(℃/%) |
22~28 |
6.4~10.2 |
Rmax(Ω) |
1.14E+08 |
1.36E+07 |
TRmax-TRmin(℃) |
100 |
121 |
瓷体密度(g/cm3) |
5.38~5.45 |
5.53~5.60 |
抗功率冲击能力 |
3次内100%分层 |
10次内有40%的产品出现阻值增大的现象 |
需要特别说明的是:采用Sr、Pb共加体系时,Sr/Pb比例以及同比例下的倍率关系既影响PTC的居里温度,也对产品的耐电压能力有着致关重要的影响;同时,对材料合成规范提出了严格的要求,否则会适得其反!笔者是在多次反复实验后,才寻找到最佳比例、倍率关系与合成规范的。
本实验所确定的Sr/Pb比例关系是0.5~3,倍率系数为1~10;
合成规范:
室温→200℃/H↑→1150℃*3H→250℃/H↓→室温
烧结规范:
室温→250℃/H↑→600℃*1H→300℃/H↑→1330℃*3H→150℃/H↓→800℃→250℃/H↓→室温
4.2产品热特性与机械特性的改善
尽管4.1的实验结果令人振奋,但产品抗功率冲击能力仍存在不稳定的缺陷。为此,笔者从陶瓷的抗热震性出发,进行了在材料中引入热传导率高、热膨胀系数小、能够达到陶瓷增韧能力材料的实验。实验主要是人氮化物(BN,A1N,Si3N4,TiN)中进行甑选,以期可以找到改善PTC陶瓷热特性与机械特性的材料或材料组合。
实验中,笔者从0.05wt%到5wt%细分添加量,分别实验了上述不同氮化物的添加效果,结论见表4。
表4
添 加 物 |
添加量范围 |
实 验 结 论 |
h-BN |
0.05wt%~5.0wt% |
添加量低于0.8wt%时,效果不太明显;添加量上升时,作为烧结助融剂的作用逐渐明显:瓷体变形,耐电大大幅度下降;合理添加量的情况下,PTC在承受功率冲击时出现分层面极端参差不齐的现象。 |
A1N |
0.05wt%~5.0wt% |
0.3wt%以下的添加量就足以降低40%以上的电阻值,并且可在不降低PTC耐电压能力的情况下使烧结温度下降1000C以上;瓷体的致密度明显提高;一旦添加量超过临界值,产品耐电压能力急剧下降,瓷体机械性能也急剧恶化;合理添加量的情况下,PTC在承受功率冲击时出现分层面参差不齐的现象。 |
Si3N4 |
0.05wt%~5.0wt% |
类似SiO2,对期望改善的性能,效果不明显。 |
TiN |
0.05wt%~5.0wt% |
随着添加量的增加,烧结温度提高;瓷体的韧性获得增强(外力作用与温度骤升情况下,瓷体不易碎裂);对PTC电阻值与耐电压能力的影响呈单调增加的趋势。 |
A1N+TiN
获得了预期的效果:瓷体的韧性改善、热传导高、热容降低(产品在手工焊接时不出现碎裂现象);合理的添加比例与添加量情况下,PTC承受功率冲击的结果——100%合格!
上述实验的配方为:(Ba89-Xmol%Sr6mol%Ca5mol%YXmol%)Ti100+Amol%O3+SiO2Bwt%+Mn(NO3)2cwt%+(A1N+TiN)Dwt%X=0.3~0.6,A=0.5~2.5,B=0.3~1.0,C=0.015~0.03,D=0.05~5.0;B、C&D按氧化物总重计算,(A1N+TiN)在合成后添加。合成规范不变;烧结温度为1320C,保温时间为1小时,800C前的降温速度为200/h。
产品的电气性能同表3中“Sr、Pb共加后,添加5mol%的CaCO3”的数据,但“抗功率冲击能力”测试结果为:10次冲击后,100%的产品阻值变化率在-5%~-10%以内。另外, 笔者还发现:CaCO3对PTC耐电压能力的影响与添加方式、添加阶段有着非常密切的关系,这是很值得注意和推敲的。
5 其它
笔者对PTC的电极、焊接工艺也进行了探索与实验,发现:磁控溅射电极有利于大幅度提高PTC的焊接强度,采用避免机械热传递的柔性焊接(如热风再流焊)有利于削弱焊接对PTC产品的性能影响, 上述两种工艺的结合可以提高PTC批量生产中抗功率冲击能力的稳定性。
6 结论
1)伏-安特性中的VImin、Imin以及阻-温特性中的α指标,可以间接反映PTC的电压效应高低。
2)CaCO3的添加量是影响PTC电压效应的一个重要因素。
3)Sr、Pb共加的BaTiO3体系,在合理的工艺条件下,有助于降低PTC的电压效应,且不会削弱PTC的耐电压能力。
4)在添加少量CaCO3且Sr、Pb共加的BaTiO3系PTC配方中,适量引入A1N+TiN改性剂可以改善PTC瓷体抗功率冲击的能力。
本文所涉及PTC抗功率冲击的失效机理分析、解决方案与实验也许存在不尽完善之处;尽管获得了实验的成功,但对于添加氮化物的效果机理只是笔者的臆断,缺乏科学的测量手段与数据来支撑, 尤其是关于瓷体热特性与韧性的判断,更是建立在原始经验的基础上,不能不说值得推敲与验证,竭诚期望能得到各位同仁的指正。 |